The production at FELSAN includes a wide variety of transformations on piping and profiles to offer a totally finished product, using the most advanced technology. Control, traceability, quality, subcontrators and logistic is monitorized by our network.
A. The most out-standing characteristics of the production system are:
- Totally automated cutting process of pipe or profile.
- Bending with latest generation numerical control systems (CNC – DNC).
- System of interior piping cleaning, “Jet cleaner” system.
- Fully Finished product delivered with end protection.
- All types of formations (flanging, countersinking, punching, swaging, etc.)
- TIG, MAG, MIG, brazing, spot welding systems, etc.
- Assembly and Incorporation of connectors, sealing rings, etc.
- Individual identification with part number by micro-percussion.
- Design and manufacture of tools, and mechanical, hydraulic and pneumatic equipments.
- Own R&D department.
B. The most commonly used raw materials are:
- Cold-drawn seamless steel EN-10305-1, EN-10305-4 / DIN2391).
- Cold-drawn welded steel (EN-10305-2 / DIN2393 y EN-10305-3 / DIN2394).
- Copper.
- Aluminium (3103, 6063, etc.).
- Stainless steel (AISI-304, AISI-316, AISI-321, etc.).
- Brass and other special materials (titanium, alloys, etc.).
- Rectangular and Square Electric Welded Precision Steel Tubes (EN-10305-5 / DIN 2395).
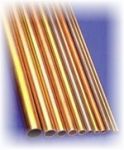
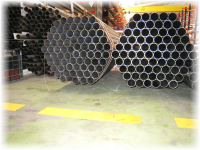
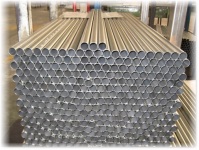
C. The most common surface coatings are:
- -Zinc plating (hexavalent chromium free coating).
- Geomet.
- Nickel-zinc.
- Galvanised.
- Cataphoresis.
- Phosphating.
- Poliéster paint.
- Epoxy paint.
D. Most common application in the automotive sector:
- Brake circuits.
- Gasoil circuits in diesel engines.
- Combustible Gas conduits (urban buses).
- Air conditioning and heating circuits.
- Engine cooling circuits and INTARDER cooling (Ø50 / Ø60 / Ø70 mm).
- Hydraulic steering, elevation circuits, etc.
- Handles.
- Body cars, truck, bus.
- Etc.